How Magnesium Hydroxide is Made
- Mac McCreless
- Jun 3, 2019
- 3 min read
The History of Magnesia and Evolution of Magnesium Hydroxide
Originally discovered by ancient alchemists, Magnesia has a rich global history as a medicinal ingredient, manufacturing component, and valuable raw mineral for neutralizing other elements. Its variants, including Magnesium, were much sought after in royal circles, mining operations, and apothecaries.
Magnesium is quite abundant in our solar system and on the Earth, as a core element in the planet’s crust as well as sea and ocean water. In the United States, it is most commonly mined in Nevada. Globally, Magnesium, in the form of Magnesite, is also mined across the world, with major deposits located in China, Europe, and Australia.
Today, Magnesium and its compounds, namely Magnesium Hydroxide, are found in pharmaceutical goods, beauty products, dietary supplements, food items, wastewater treatments, fertilizers, animal feed, and an ever-increasing number of complex technical and manufacturing processes.
Magnesium Hydroxide, chemically named Mg(OH)2, is an inorganic compound most often distributed in powdered or slurry form. It can be produced using three key methodologies: its natural occurrence as the mineral Brucite, through the hydration of Magnesium Oxide, and through precipitation of seawater or brine.
Examining Brucite as a Natural Source of Magnesium Hydroxide

Brucite was discovered in 1824 in New Jersey as a tabular crystal of blue/green hue. As a naturally occurring compound, it must be located and mined, which can be a disincentive compared to less expensive and more convenient synthetic alternatives. Based on current mineral maps, the largest known deposits of brucite ore exist in China and eastern Russia.
Natural brucite is the rarest type of magnesium hydroxide due to the issues regarding access and cost, but brucite ore also has several notable benefits, including high magnesium percentage compared to other available raw materials, reduced manufacturing time, and zero carbon dioxide content, which can contribute to climate change when it is released during mineral processing.
Synthetic Manufacturing of Magnesium Hydroxide through Brine or Seawater Precipitation
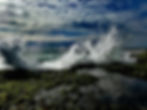
A more common way, accounting for approximately 60% of the global supply of Magnesium Hydroxide, is precipitating the solution from a combination of seawater or brine and lime (or Calcium Oxide). This method was first undertaken in 19th century France and has since been perfected by the largest global synthetic producers: China, Israel, and the United States - specifically California, Michigan, Delaware, and Utah.
Both brine and seawater must be manually gathered, often in a constructed sump cavern. Seawater can vary in consistency, containing a variety of organic compounds that can complicate the precipitation stage. Brine originating in a well or a lake can also differ depending on the chemistry of surrounding rocks and other geographical formations. These initial materials will need to be purified to ensure the ideal composition prior to mixing.
In addition, this process, completed in a series of agitating reactors and supplemented with washing and filtration, has very specific temperature, time, and pressure requirements, which ultimately impact the quality of the resulting Magnesium Hydroxide. Because of these variables, the final product requires significant testing to ensure the meeting of quality and purity standards.
Hydration of Magnesium Oxide to Create Magnesium Hydroxide
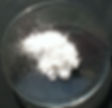
A final option for crafting Magnesium Hydroxide is through the hydration of Magnesium Oxide. Magnesium Carbonate (Magnesite) is calcined at high temperatures, losing over 50% of weight to CO2, to produce Magnesium Oxide (MgO).
Creating Magnesium Hydroxide involves adding water (H2O) to Magnesium Oxide, often in an agitation tank to accelerate the reaction, which is exothermic (heat producing) and must be cooled.
This is the preferred procedure to create Magnesium Hydroxide slurry, though the end product must be diligently monitored for both viscosity and solids content as well as particle size.
The Garrison Minerals Difference
Garrison Minerals has the expertise and industry network to procure Magnesium Hydroxide utilizing all three methodologies: the mining of naturally occurring Brucite or Brucite Ore, the precipitation of brine or seawater, and the hydration of Magnesium Oxide.
All other Magnesium Hydroxide suppliers in the market today typically only pursue a single methodology, two at most, where Garrison Minerals actively and successfully supplies Mg(OH)2 in all three ways – guaranteed to find the technique that will fit your organization’s budget, production timeline, and quality and sourcing standards. Combined with superior customer service, material knowledge, logistics and project management, Garrison Minerals will find your ideal solution.
-------------
To learn more about these methods and the supply process, contact Garrison Minerals and speak directly with a Magnesium Hydroxide consultant.